What is Lean Six Sigma: A Complete Overview
Study SkillsWhether you’ve heard of this as part of the jargon during project meetings and wondered what Lean Six Sigma is all about, or you have peers and LinkedIn connections that have a certification in Lean Six Sigma and you’re wondering if you should get certified as well, this article is just for you.
This article is aimed at being simple, short, and practical. By the end of this article, you will have learned what exactly Lean Six Sigma is, beyond the conference jargon, how Lean and Six Sigma are actually different, the tools used, and the certifications. But first...
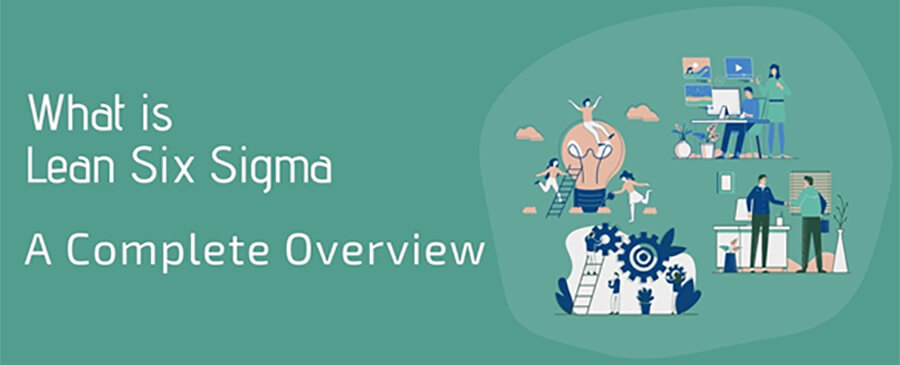
A Lean bit of history
It all started with Motorola developing the Six Sigma program to tackle the traditional practices that left much to be desired when it came to quality. Little did anyone know that this would spur a new wave of innovation and spring an entirely new field of study - quality management.
Motorola’s success, to the tune of $16 Billion in savings, set an example to companies from every industry - from manufacturing to health care - that quality management was a serious money-saver. Six Sigma spread like wildfire.
On the other hand, Lean found its beginnings in the assembly lines of Henry Ford’s automobile factory. From parts that could be interchanged to the first moving conveyor, efficiency was for the first time designed into the production line itself. This design of systems led to achieving outcomes of high-quality while keeping the cost low.
And just like Six Sigma’s widespread adoption, Lean gained a reputation quickly as well.
But it’s easy to conflate the two in terms of their goals and the benefits their adoption offers.
The difference between Lean & Six Sigma
When it comes to Lean, think efficiency. All of the efforts in Lean practices is to minimize delays, wastage, and errors. On the other hand, Six Sigma concerns itself with quality and consistency.
While Six Sigma tackles the issue of manufacturing products and services that make meeting quality standards a run-of-the-mill affair, ensuring that - by analogy - your go-to restaurant makes your favorite dish just like when you had it for the first time, Lean makes your service itself, better.
What is the oft-repeated phrase DMAIC?
Anyone even vaguely familiar with the subject of Lean Six Sigma knows of this acronym.
DMAIC is essentially a framework that is adopted by quality management professionals who use Lean Six Sigma to set up their company’s processes.
Here is a quick breakdown of each step along with what they stand for in the acronym.
Step # 1: Define - Identifying the benefits and costs whilst actively considering the problems and opportunities involved is the first step of the DMAIC framework. This is done from a business perspective.
Step # 2: Measure - Now that the feasibility and justification for beginning a new project have been established, it’s time to set up tangible, measurable goals. Goals such as “improving customer service” or “reducing assembly line delays” are vague. Instead, establish goals along the lines of “improving customer service by 20%” (which would require you to establish what that improvement is, really) and “reducing assembly line delays by an hour” (which leads to follow up questions on where exactly is there room for improvement).
Step # 3: Analyze - This step is where the brainstorming really takes place with regards to how the targets can be met. Various solutions are posited and compared.
Step # 4: Improve - From hiring and training resources to acquiring new equipment to setting up new processes and procedures, this step is all about implementing the solution finalized in step 3.
Step # 5: Control - Assuming that step 4 follows through successfully, step 5 is then concerned with maintenance - to see to it that the process is standardized and any changes in it are a result of conscious decisions only.
Lean Six Sigma also provides a set of exhaustive tools that help follow the above steps from beginning to end of any project, large-scale or small.
We next look at the Lean Six Sigma tools.
Lean Six Sigma Tools
There’s a lot to be said about each tool - and there are many - but the aim of this section is to acquaint the reader with what tools are at the disposal of a trained Lean Six Sigma professional and what he/she can achieve with them. We won’t get into each tool in detail as that is beyond the scope of this overview guide to Lean Six Sigma. However, here’s a quick overview of eleven such tools.
-
Systems
This is a tool to map products and services as outputs from a given set of inputs which are transformed to the former by processes.
-
SIPOC Diagrams
When embarking on a project, a SIPOC diagram helps map out suppliers, inputs, processes, outputs, customers.
Voice of the Customer
From online feedbacks to interviews and questionnaires and comments on Facebook, Amazon, Instagram, etc, i.e. the voice of the customer is analyzed to design or redesign initiatives and processes.
Critical to Quality
This addresses the processes from the angle of critical needs, what drives the quality to be delivered and what the performance requirements are in order to meet the project goal.
-
Value Stream Maps
A graphical tool to pay specific attention to delays incurred at each step of the process visually.
-
Cost of Poor Quality
This involves evaluating the expenses incurred as a result of poor quality which could lead to the return of goods and tarnishing of the brand, amongst other things.
-
Multi-Vari Chart
While not wound up in complicated statistics, a multi-vari chart has markings of mean and variation of each process. This is a quick marker of a process’ performance at a snapshot.
Sampling
This is a method to gain a ballpark measurement of the audience. While not exact, when done correctly can give a good reflection of the population.
-
Process Control
A means of ensuring that the process doesn’t vary beyond a certain amount. This is to see to it that the deviations of a process from its ideal form are measured and kept under control.
FMEA
FEMA, short for Failure Mode and Effects Analysis, is all about creating contingency plans, from spotting potential mistakes and pre-emptively troubleshooting them.
Design of Experiments
From A/B testing to other statistical approaches of experimentation, there are various ways of designing experiments to test and elicit knowledge that can help make key decisions.
Further Reading from Skills You Need
The Skills You Need Guide to Leadership eBooks
Learn more about the skills you need to be an effective leader.
Our eBooks are ideal for new and experienced leaders and are full of easy-to-follow practical information to help you to develop your leadership skills.
Lean Six Sigma Certifications
When it comes to becoming a professional lean six sigma certified quality management professional, there are four tiers of certifications:
- The Yellow Belt - achieving this allows you to work in, and assist, a team that uses Six Sigma.
- The Green Belt - covers the entire corpus of Six Sigma and can help spearhead processes while working under the direct supervision of Black Belt professionals.
- The Black Belt - you develop proficiency in the complete Six Sigma body of knowledge and will be able to lead small scale projects.
- The Master Black Belt - in addition to developing proficiency, you also have the capability to manage large-scale projects, supervising everyone from Yellow to Black Belt holders.
With this, we reach the final point to address in this guide. Which of these certifications should you take?
There isn’t a straightforward answer to this, however. For someone new to business processes entirely, the Yellow Belt is where you should begin your journey. However, if you can put in the dedication and can take up the challenge, you can directly take the Green Belt with a month or two of preparation. Attaining Black Belt status, on the other hand, will take far longer, depending on a candidate’s prior knowledge of quality management and Lean Six Sigma,
About the Author
Amelia Emma is a Content Marketing Manager with 6 years experience in developing unique and research-driven content on professional certification courses like PMP, ITIL, Lean Six Sigma and many more.